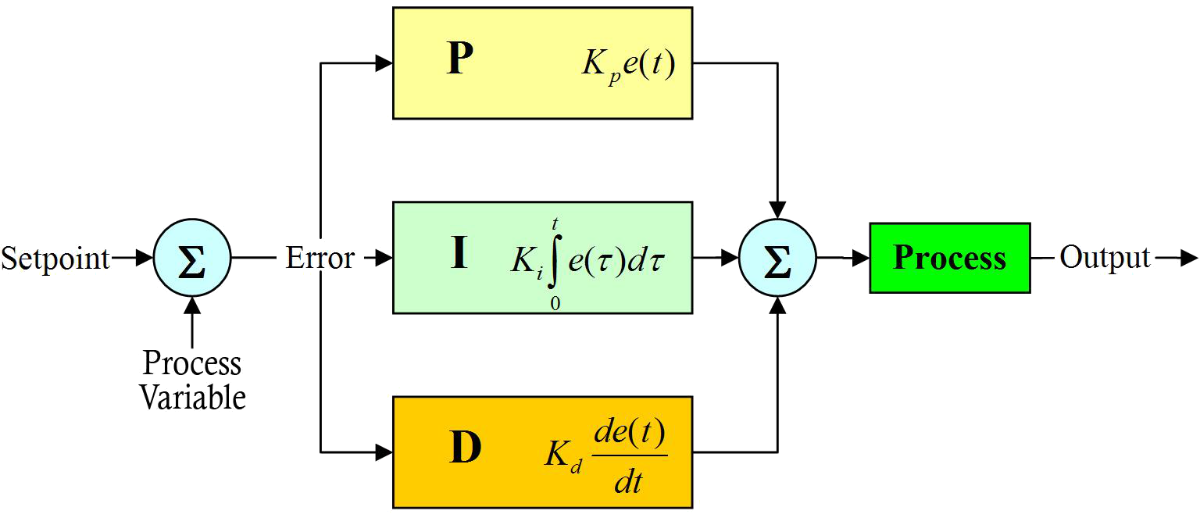
Process Instruments (Pi) are increasingly seeing water engineers and technicians relying on their PLC’s PID auto-tune feature. Many are becoming frustrated that the auto-tuners are unreliable when it comes to water processes. Sometimes the auto-tuned PID settings work, but then something changes in the process and the PID control no longer functions correctly.
In this Focus On, Pi aims to outline how PID auto-tuners work and why they are often unsuitable for complex water treatment processes. We also give a brief introduction to some of the principles of tuning a PID manually.
Did you know that…
…auto-tuners are not effective at tuning processes with long loop times?
…the CRONOS® and CRIUS® have many built-in PID safety features to make control easier and safer?
…PID loops can often be tuned remotely, meaning huge savings on site visits and travel time?
What is PID tuning?
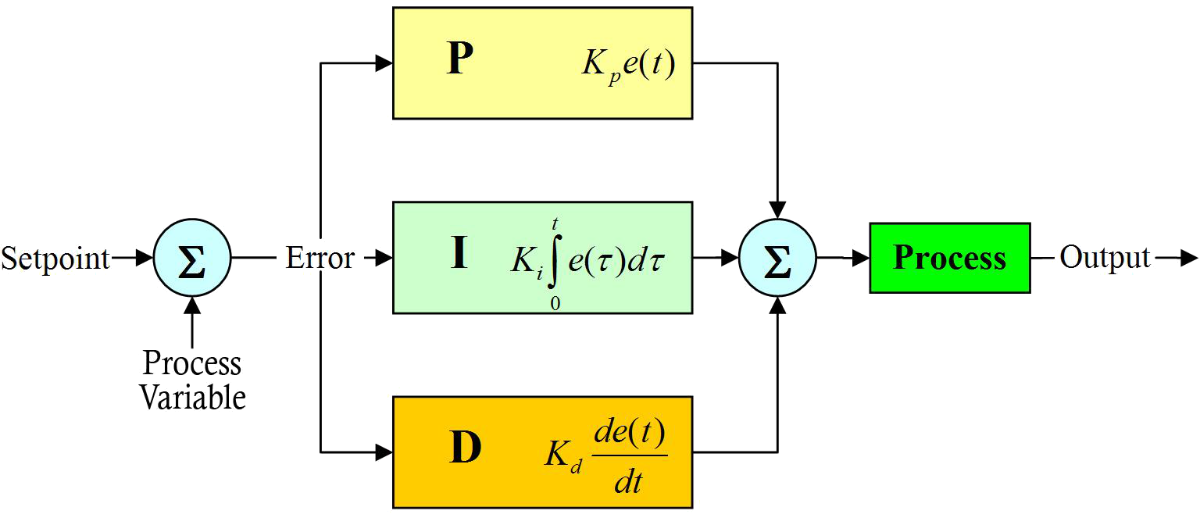
A Proportional – Integral – Derivative (PID) controller is a control loop feedback mechanism widely used in industrial control systems. PID controllers allow a system to continuously and automatically modulate a control mechanism (e.g. a dosing pump, a valve, motor speed), to attempt to achieve a desired setpoint.
There are a myriad of ways that a PID controller can be ‘tuned’. In a very basic PID controller, the operator can choose how much of their control should be based on P, I and D. In reality, D is almost never required in water processes due to the nature of the control loop.
This is generally the task that ‘auto-tuners’ undertake. They make small changes to the ratio between P, I and D control, track the response, decide if the change is good or bad, and then change again.
What is the auto-tune doing?
So what the auto-tuner is doing is changing, measuring, and changing again; which can work perfectly on processes with a very short loop time (time between a change and a response from the system), the auto-tune making many changes in a short amount of time. The changes cumulate into a ‘tuned’ PID system.
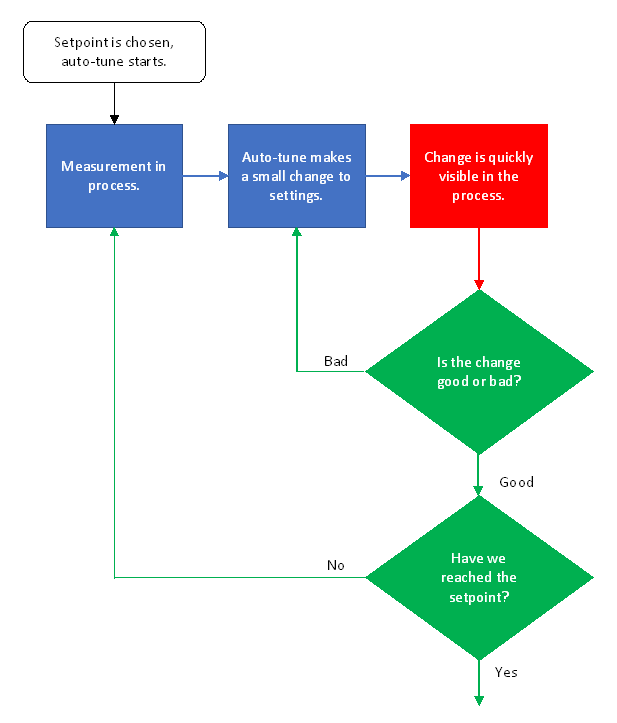
On the right is an example system of a PID auto-tune.
In the diagram, we can see that for the system to work, the box in red is a crucial part of the process. If the change brought on by the PID auto-tuner isn’t visible quickly enough, it may affect the way the auto-tuner categorizes the change (good or bad), or won’t give the auto-tune the opportunity to make enough iterative changes to bring a complex water system under control.
The good news
There is good news for water technicians and engineers and that is that Pi are here to help. All our salespeople are application specialists and are all capable of helping you manually tune a PID controller for your processes. Our CRONOS® and CRIUS® controllers are both capable of delivering excellent control in many processes, and have many built-in PID features to help make your process more controlled, robust and safe.
Where to start with PID tuning
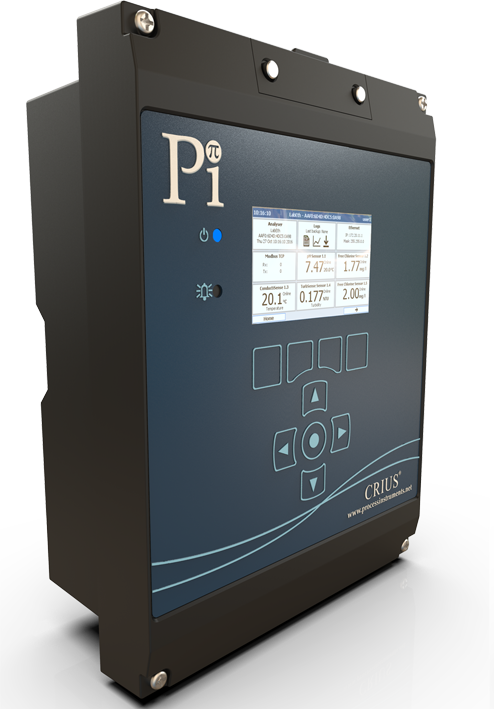
In many ways, the auto-tuners mimic plant engineers making adjustments and tuning their PID settings. They simply lack 2 key components;
- Patience – because the loop times are so long, it will take time to tune a PID loop.
- Context – no auto-tuner can account for blocked dosing lines, or 2 identical pumps that are improperly calibrated and output different volumes, or seasonal changes in measured parameter concentrations. Context is incredibly important in tuning a PID loop.
With this in mind, here is how our engineers approach PID tuning on our instruments;
- Check the measurement and output method are all working properly. This includes any calibration on the probes and on the pumps as well as checking that the dosing lines are clear.
- Consider the loop time and change the PID’s Update Delay. This changes how often the PID algorithm makes a change to the output.
- Start small and ramp up. Start with the P control and slowly increase the P factor until it is changing the measurement in a satisfactory timeframe. If you can get a good level of control with just P then that’s excellent. There is often no need to overcomplicate things past this. The addition of I and D components is often unnecessary.
- If you have wild or erratic control lower the P until the control is stable, even if it doesn’t reach your setpoint then add some I control.
- Always aim to have I as low as you can get away with, as I can cause more problems with control than it solves.
Once you have the basic P and I ratio sorted, or if you are unable to get the P and I into control, it is worth considering these additional settings which will help make your control scheme more robust and safer.
- Min/Max Output – restricts the range that the PID can work within, which can stop potential over- and under-dosing. This setting may also reduce the ability of the PID loop to respond to changes in the water.
- Start Mode – allows the process to be dosed using a flow proportional value or a manual percentage value, during a predetermined start up period. This is often used to get the process up and running before going into PID control.
- Ramping – smooths the start-up of the process where the error between the measured value and setpoint may be very large (which can cause erratic overshoot and overcorrection).
- Bumpless Transfer – smooths out the process of switching between manual and automatic control.
- Integral Wind Up Protection – puts a limit on the effect of I because I looks at error over time. A very small error over a large amount of time can result in a very large I output resulting in erratic control.
- Overfeed Protection – protects against the failure of other equipment, such as failing pumps or blocked dosing lines. This puts the control into alarm if the controller is calling for dosing but is seeing no change.
How our products can help
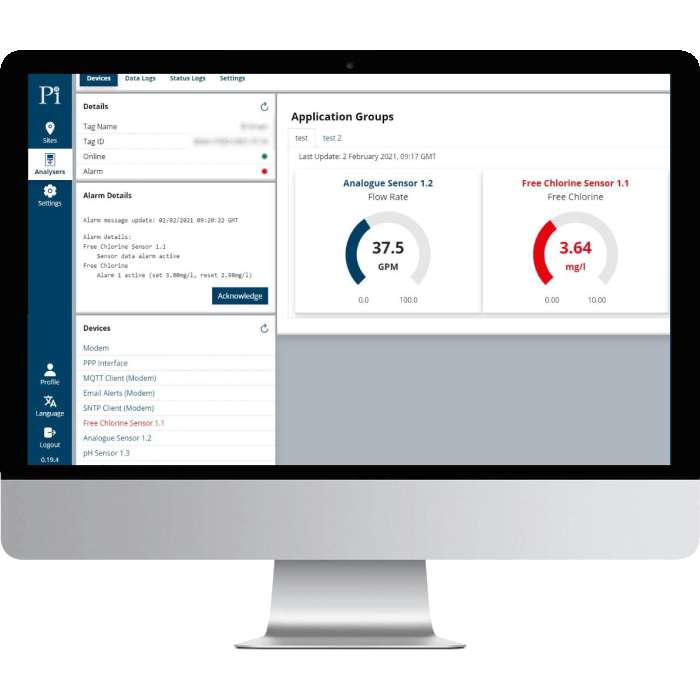
Even armed with all this knowledge, PID tuning can be a bit of a dark art. What works on one site may not work on another and even experienced engineers sometimes call us for help.
One of the ways we can help is using our remote access system Control InSite®. Our Remote Access portal (Control InSite®) allows people with the appropriate security clearance to make changes to settings and observe measurements from their desk.
Sales Manager, Dr. Rob Paramore, recently described his experience of changing a customer’s PID settings (at their request), whilst talking them through what he was doing on the phone: